3D-Printed Theatre Costumes
completedFellowship
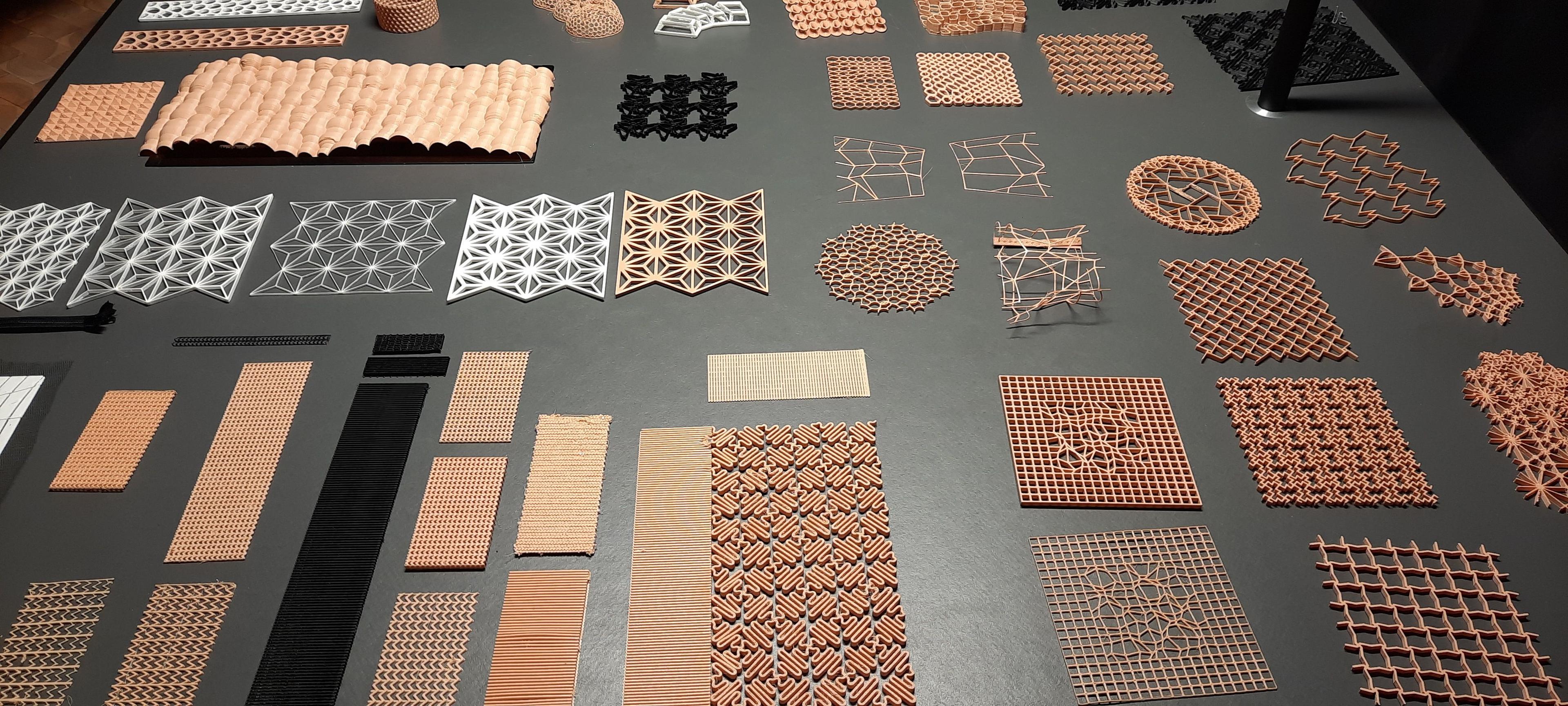
SummaryYvonne Dicketmüller's fellowship project focuses on 3D-printed theatrical costumes. The goal is to explore modern manufacturing techniques, including 3D-printing, new materials and design software, to generate new aesthetics for the field of costume design.
Introduction to Digital Fabrics
How To Make 3D-Printed Costumes
During my fellowship at the Akademie für Theater und Digitalität in Dortmund I have been researching the possibilities of 3D-printed costumes. That is costumes that are produced entirely with the method of 3D-printing.
At the beginning of my research I first familiarized myself with both the material that I was going to use: flexible TPU filament, and the machine with which I was going to work: a Prusa i3 MK3S 3d-printer. Next, I started to learn to design with the software which I had chosen for my project: Rhino 3D.
I printed several sample pieces of the designs that I made. All of them were roughly 12 cm x 12 cm and had varying thicknesses.
By printing and then handling the samples, I built an understanding of the material properties a 3D-printed costume would have. I learnt that some of my designs, when printed out, behaved more like woven fabrics while others had the feel, touch and textile qualities of knitwear.

3D-Printed Costumes Based on Regular Sewing Patterns
After I had built a first understanding of how I could design and print my own TPU-fabrics, I went on to explore how I could print a complete garment that could be worn by an actor or dancer on stage. I decided I would try to use a regular sewing pattern, digitize it so that I could use it in Rhino, and then print out the different garment pieces one by one. Given the compact size of my printer's print-bed, I had to print some of the larger parts of the garments like sleeves, front or back parts in several pieces that I later fused together.
The first costume that I 3D-printed in this way was a skirt, followed by a tank top.

With the tank top I learnt that I might need to make adjustments to the regular sewing patterns if I wanted to create fully functional 3D-printed garments. Unlike the regular tank tops which are made of stretchy knitwear and stretch sufficiently when you put them over your head, my tank top was designed with a pattern that resembles a woven fabric. Accordingly, my 3D-printed tank top didn't stretch enough to fit over the shoulders.
After this experience I started to think of ways to make my 3D-printed garments more “wearable”. I explored ways of integrating regular zippers and buttons into my 3D-printed costumes and eventually developed a new top with a zipper and a button in the back.

3D-Printed Costumes Based On A Pattern Derived From An Existing Garment
Using an existing garment - in this case a jacket - I tried to derive a pattern that I could then use just like the sewing patterns above to make a 3D-printed piece of clothing. I traced the outlines of my jacket, made a paper model which I then photographed and imported to Rhino. In Rhino, I decided on D-print the individual garment pieces.
After about one week of printing time, I held all the pieces of my jacket in hands. I assembled the jacket and made adjustments where necessary.

3D-Printed Costumes Based On The Draping Technique
Towards the end of my research, while I was printing the jacket, I started to explore the technique of draping. At that point I had already printed one of the sleeves of the jacket and thus had a large piece of 3D-printed TPU-fabric lying around. With this fabric I approached my mannequin. I draped the 3D-printed textile over the body and explored how I might be able to make a top.
With the draped sleeve-fabric pinned into place, I took measurements and made my very own sewing pattern curves directly in Rhino. I went on to print the pieces - one front and one back piece - and went back to the mannequin with them. I pinned the front and the back of my new top onto the mannequin, then I started to develop some ideas as to what the sides of the top might look like. I designed the side pieces in Rhino. Once printed, I assembled the top.

Findings
The 3D-printed costumes that I made during my fellowship have their very own aesthetic appeal. They have a lace-like appearance, a soft touch and feel nice even when worn directly on the skin. Printed with a rubbery material, TPU-filament, they are a little more on the bouncy side which helps to make the garments “come alive”. At the same time the 3D-printed fabrics can have a certain stiffness so that they can refuse themselves to certain movements. I find this to be a very interesting characteristic, and I am hoping to explore this further in future projects with actors and dancers.
If you want to learn more about my project or f you are interested in a collaboration, please feel free to contact me: http://www.yvonnedicketmueller.de/